

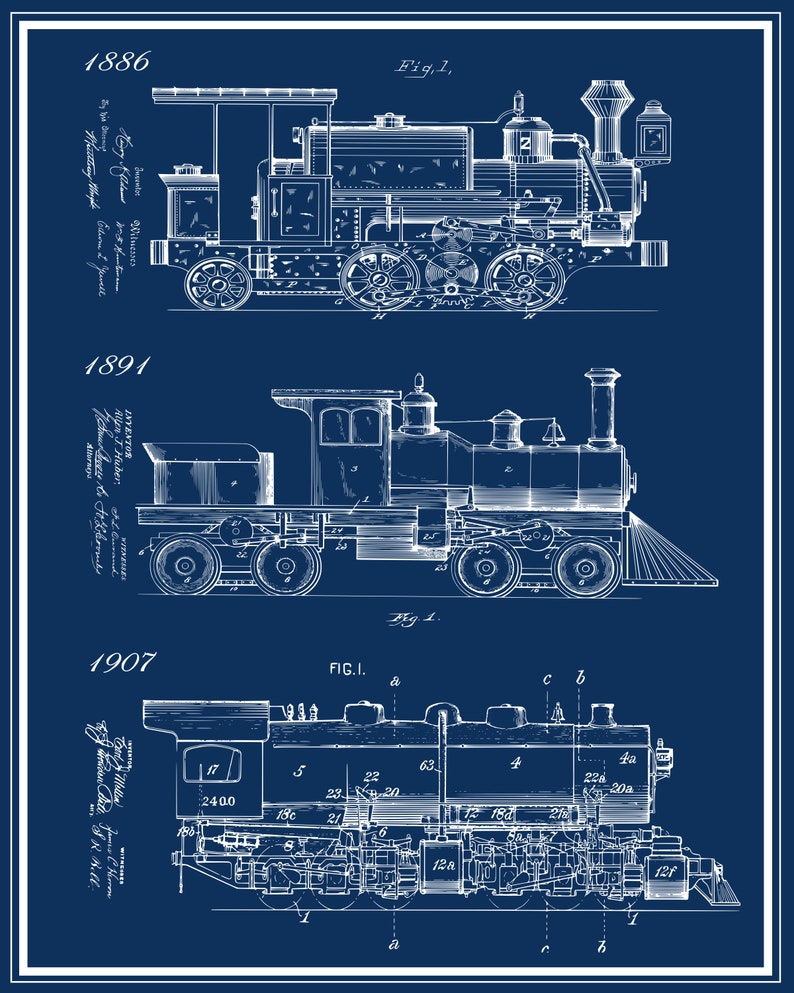
In addition to the BIONEQXX rear-floor casting, another BIONICAST component that features in the VISION EQXX is the damper domes which accommodate the suspension components at the front of the car. The beauty of the one-part BIONEQXX casting is the ability to pair this with functional integration within an extremely lightweight single component rather than an assembly of multiple parts joined together. The most important of the structural criteria is the need for very high stiffness and excellent crash performance. In line with the laws of nature, where there is no load there is no need for material. Taking their cues from organic forms, the development engineers sought to use material only where necessary for structural function, i.e. Furthermore, the team created this impressive and manufacturable one-part casting in just four months. The result is optimum functionality packaged within the compact dimensions of the available space.
#Blueprint printing software#
It was developed in-house by Mercedes-Benz using entirely digital techniques and a software approach that is utterly unique within the automotive sector. Yet other parts, even smaller ones such as the suspension mount, were also cast from a 3D printed mold.Ĭurrently the largest aluminum structural casting at Mercedes-Benz, BIONEQXX is the major structural component at the rear end of the VISION EQXX – the rear floor. To produce the BIONEQXX part, which is the largest aluminum cast ever made by Mercedes, the company used a giant 3D printed sand mold that was likely created using an internal voxeljet machine.
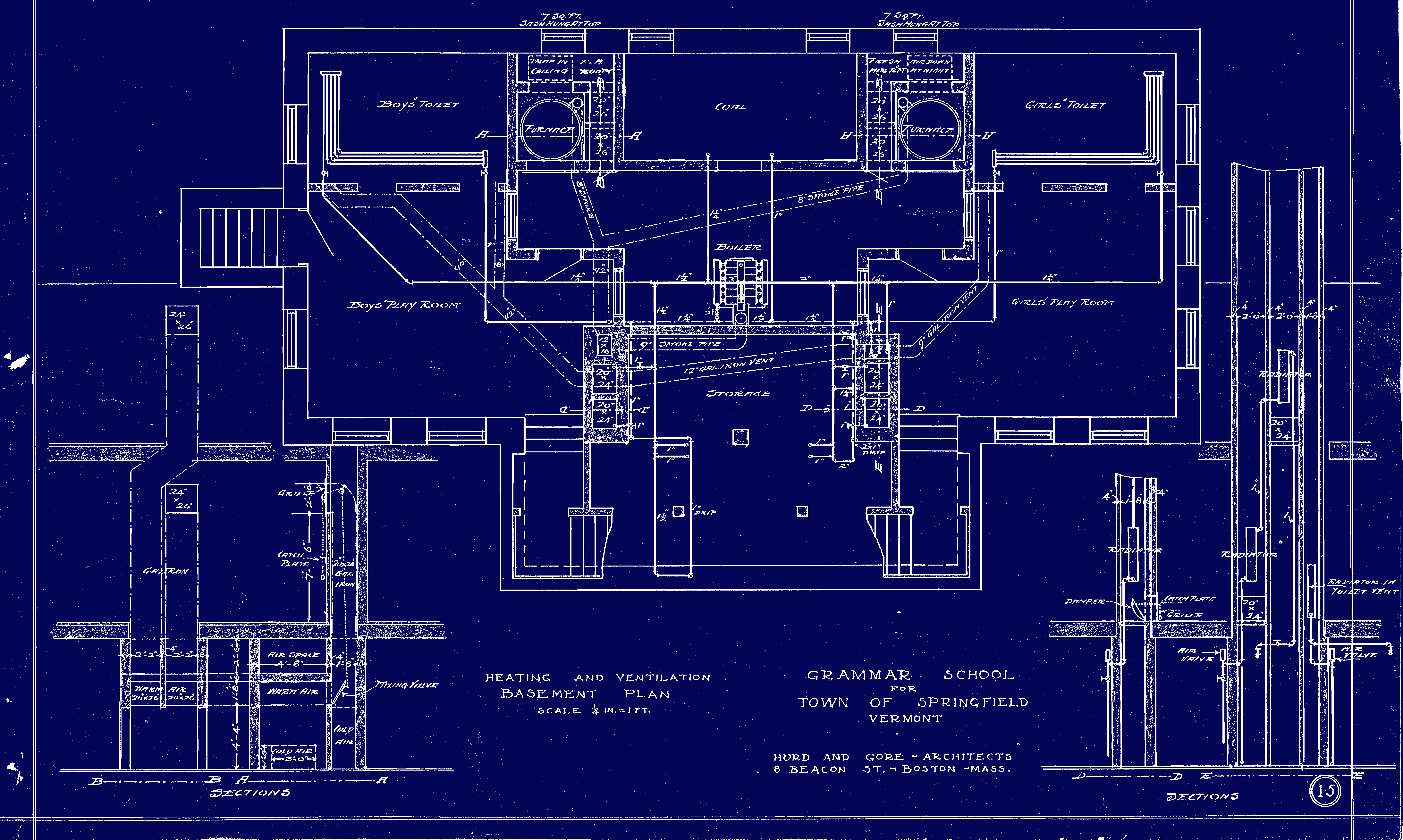
As shown in the video below (go to minute 13:00), the Mercedes VISION EQXX’s entire rear subframe, which the company refers to as BIONEQXX, is built by consolidating over 70 parts into a single, bionically engineered, optimized aluminum cast. Inspired by natural forms and in partnership with innovative start-ups, engineers used advanced digital tools to lower weight and reduce waste by removing excess material assisted by 3D printing. The VISION EQXX stands for major new advances: it sets new standards in terms of energy efficiency and range in real-life traffic and revolutionizes the development of electric cars. The car has a range of more than 1,000 kilometers with an outstanding energy consumption of less than 10 kWh per 100 kilometers. The VISION EQXX is how Mercedes-Benz imagines the future of electric cars. With that, it underlines where our entire company is headed: We will build the world’s most desirable electric cars.” Ola Källenius, Chairman of the Board of Management of Daimler AG and Mercedes-Benz AG. The VISION EQXX is an advanced car in many dimensions and even looks stunning and futuristic. It has a range of more than 1,000 kilometers on a single charge using a battery that would fit even into a compact vehicle. Just one-and-a-half years ago, we started this project leading to the most efficient Mercedes-Benz ever built – with an outstanding energy consumption of less than 10 kWh per 100 kilometers. “The Mercedes-Benz VISION EQXX is how we imagine the future of electric cars. This includes advances across all elements of its cutting-edge electric drivetrain as well as the use of lightweight engineering through advanced 3D printing processes, and the use of new sustainable materials (also 3D printed). It demonstrates the gains that are possible through rethinking the fundamentals from the ground up. The VISION EQXX is the result of a mission we set ourselves to break through technological barriers across the board and lift energy efficiency to new heights. They are working intensively to take range and efficiency to a whole new level. Driven by the idea of zero impact and highly responsible use of green energy, we inspired our engineers to go above and beyond. The new Mercedes VISION EQXX concept has been hailed for range and efficiency that are set to define the electric era.
